Hi meet
Interim Management
Mark Akers
With nearly 40+ years experience in the food industry, I excel at problem-solving, driving change, and improving operations. Skilled in lean manufacturing, I ensure efficiency while upholding health and safety standards. Confident, reliable, and focused on results.
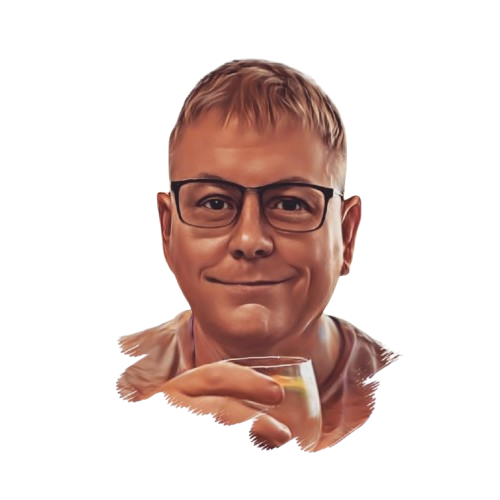
my career
2023
McCain Foods and Florette
2024
Harrods London and Avara Foods
2025
Branston’s Potatoes and the Compleat Food Group.
My Key Skills
A strong decision maker with nearly 40 years’ experience in the food industry, able to focus on the bigger picture and overall company targets. Takes great pride in making things work and finding solutions with the resources and budgets available. Confident and reliable with an appropriate sense of humour, enjoys making change happen within guidelines and constantly developing and working on continuous improvement projects using lean manufacturing techniques and world class manufacturing initiatives to improve the day to day running of the factory in accordance with health and food safety.”
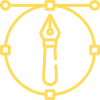
TECHNICAL KNOWLEDGE
Skilled in lean manufacturing, I optimize production while ensuring efficiency, quality, and food safety compliance.

CHANGE MANAGEMENT
Skilled in driving change, I implement improvements while ensuring efficiency, compliance, and smooth transitions.
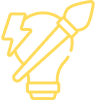
PEOPLE MANAGEMENT
Experienced in leading teams, I foster collaboration, drive performance, and ensure a productive work environment.
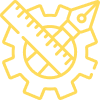
PROBLEM SOLVING
Strong problem-solver, I find effective solutions, optimize processes, and drive continuous improvement.
Explore my Resume

Biography
I’m an experienced Interim Manager with nearly 40 years experience in the food industry, specializing in production management, process improvement, and lean manufacturing. I thrive on problem-solving, driving efficiency, and ensuring top standards in food safety and quality.

Qualification
I hold NVQ in Food & Drink (Level 1 & 2), HACCP Level 2, multiple food safety certifications, and management training in health & safety, lean manufacturing, and process optimization.
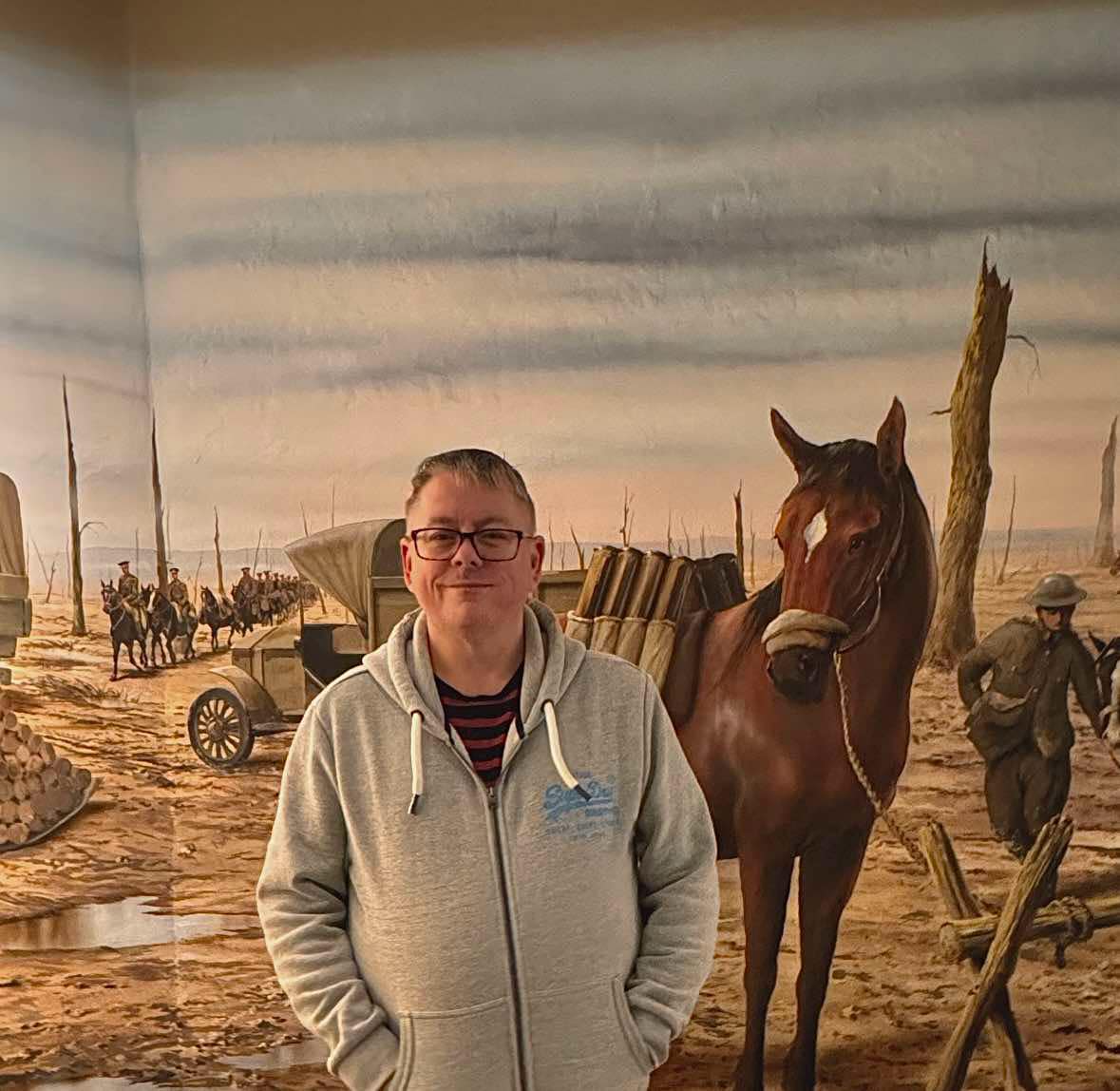

Experience
I’ve led production teams, optimized processes, and implemented continuous improvement strategies. My focus is on efficiency, quality, and food safety, ensuring smooth operations in fast-paced environments.

Contact
If you’re looking for an experienced Interim Manager with a strong background in production management, process optimization, and team leadership, feel free to reach out.
QUALIFICATIOS
NVQ in Food and Drink level 1 and 2
Byrne Fleming Management
Career Track Professional Supervision Skills
Supervisor’s Training in Chemicals
Chemical Handling and Safety Awareness
Essential and Intermediate Food Hygiene Certificate
Disciplinary and Absence
Recruitment and Interviewing Skills
3 CSEs, Including Maths and English
HACCP Awareness Level 2
Level 2 & 3 food safety
Multiple first aid qualifications
My Professional Journey
April 25 – Present • Avara Foods • Interim Production Support Manager.
My role at the Avara Foods is to help and support a very busy ready meals business, supplying all the major supermarkets with top class Products, i will also be heavily involved in training and coaching Process leaders and Shift Managers to reach their career goals, this is the 4th time i have worked for Avara and with 10 extension’s to my contracts so i know the Business very well.
Feb 25 – April 25 • The Compleat Food Group • Interim Factory Manager.
My role at the Compleat Food Group is to run a very busy night shift as the Factory Manager making the new Scotch egg and other savoury products for all major supermarkets, this product was transferred from their sister site in Dorset due to closure last year, this is a new start up for the site here at Milton Keynes so training and coaching staff is key.
Nov 24 – Feb 25 • Branston’s Potatoes • Interim Production Manager.
As the Production Manager within Branston’s, I am responsible for the day to day running of a very busy Potato Processing plant, my focus in this role was to be a safe pair of hands over the Christmas period providing potatoes to Tesco and Business to Business, also coaching and mentoring employees.
June 24 – Nov 24 • Harrods London • Interim Production / Project Manager.
As the Production Manager within Harrods, I am responsible for the running of both hot and cold kitchens providing all the food to the 32 Harrods restaurants in the store.
My focus in this role is to bring Harrods into the future state as a Production Facility and not a kitchen due to a potential move off site in the future.
The Production Manager role is heavily involved in food safety, quality and customer satisfaction, and working with top chefs to achieve the gold standard status you would expect from this prestigious department store
Jan 24 – June 24 • Avara Foods Ltd • Interim Production Support Manager.
Currently running a very busy afternoon shift seeing through new product launches with M&S, Lidl, Tesco, and Asda with the transaction of products from our sister site.
Due to the refurbishment of our sister site all staff were transferred to our Wednesbury site along with all the products for 3 months.
Due to all the staff from early April going back to our sister site we are currently in the process of training and coaching over 150 agency staff to gain the skills needed to continue our new launches with all the major supermarket chains.
Due to the nature of the business a very ‘Hands on approach’ is needed to maximise efficiencies, focusing on-line speeds and plan attainment ensuring we supply the quality of all our products to our customers.
Sept 23 – Jan 24 • McCain Foods • Interim Production / Factory Manager.
Reporting into the Plant Manager, as part of the S.L.T. I am responsible for the day to day running of a very busy Potato Processing Plant.
SQDC is a big part of the K.P. I’S here at McCain Foods Limited.
Working with all Departments daily to optimise results.
Plant Manager cover during company commitments and holidays.
Leasing with all major stakeholders within the business daily including, H.R. Engineering, Plant support, Health and Safety, and other sites within the McCain Group.
Reporting Performance to Group on a daily / weekly basis through Teams meetings and face to face meetings.
July 23 – Sept 23 • J.L.R • Interim Health and Safety Consultant.
Working as a Health and Safety Consultant at Jaguar Land Rover, supporting a major shutdown focusing on Contractors Safety and welfare when commissioning new robots and lines.
Part of QSC group.
6Jan 23 – June 23 • Florette / Agrial U.K.• Interim Manufacturing / Deputy Site Manager.
Responsible for managing the day-to-day operations on site, leading the manufacturing team across the whole of the production life cycle, Direct responsibility for safety, quality, productivity, and waste within the manufacturing operation. A driver of change, constantly seeking opportunities for improvement and will deputise in the absence of the Site Manager / General Manager.
Managing the Production team via 5 Area Managers to ensure that all products are produced in line with specifications and within agreed timescales.
Ensure production procedures are carried out to comply with quality & HACCP systems.
To manage the capacity of the factory, maximising yield, and productivity.
Ensure that company and statutory H&S regulations and hygiene requirements are always adhered to.
Creating a performance culture and developing talent.
The management of customer visits to ensure compliance with required standards.
To provide direction, motivation, and support through effective management of direct reports.
To work closely with the Site Manager on the future development of the factory.
Out of hours support when required.
Part of the SLT.
July 22 – December 22 • Warp Snacks• Interim Night / P.M. Manager.
Started my time at Warp Snacks running a start-up night shift, I was responsible for recruiting staff for skilled roles within the business, staff coaching and mentoring is a key part to my role, after 4 weeks I was asked to run the P.M. shift to improve efficiencies within the Production areas, I have been heavily involved in the S.I.C. process within the business and worked very close with the senior team to ensure we get the right process flow.
May 22 – July 22 • Charlie Bigham’s • Interim Night Site Manager
Responsible for all Operation functions on site during the night, on a very busy ready meals business, helping support all areas including preparation, assembly, and cooking until a permanent night manager is found.
Jan 22 – April 22 • Orchard House Foods • Interim Operations Manager Low Care and High Care and Projects.
Responsible for all Operation functions in a very fruit business, this includes Preparation, line Production, Wash Hall and Despatch, this role is heavily based on various K.P.I.’S and achieving Plan Attainment and Customer orders, Quality is a major part of my role ensuring that our customers receive the best Product all the time, during my time ay Orchard House Foods I have worked both shifts to achieve the same standards and performance / efficiency’s.
Sept 21 – Dec 21 • A.M. Fresh Ltd • Interim Performance Manager
Working in a busy pack house packing citrus and grapes for all major supermarkets, responsible for improving K.P. I’S until the business finds a permanent Manager for this position.
May 21 – Sept 21 • Ferndale Foods Ltd • Interim Operations / Process Management Support / Interim Intake Manager
Working between Process Development and Operations to make the Process of new ready meal trials a smooth process, working closely with new product launches and looking at ways of increasing our Production to 1.8 million meals per week by September, also standing in for the current Intake Manager due to sickness.
October 20 – February 21 • Fletchers Bakery Ltd • Interim Manufacturing Manager / Continuous Improvement Projects Manager.
Responsible for the day to running of a very busy bakery, my main remit was to set up S.I.C. boards on all lines to improve efficiencies and improve moral on the lines, during my time at Fletchers I worked with the team as the link between the Operations Manager and the Front Line Mangers and in turn improved communication within the business, this was a short term contract due to filling the gap until the new Manufacturing Manager starts in January, this contract was extended until mid-February due to high growth in orders and being covid compliant.
May 20 – September 20 • Avara Foods Ltd • Interim Management Support
My role at Avara Foods is Interim Management Support, this is my second time working for Avara Foods, running all retail and BBQ lines during their peak period and while they search for a Permanent Manager, this contract was originally for a 2 month period but was extended from July until September, during my second time at Avara Foods I was responsible for running any Departments that they needed help to improve, looking at labour variances, cost savings on machinery and working alongside the Production Manager to improve the day to day running of this very busy poultry processing site.
April 20 – May 20 • Morrison’s Flower world • Interim Management Support
Helping feed the nation making food boxes for the elderly and vulnerable during this time with the covid 19 pandemic, When the food boxes started to slow down a bit, I was transferred to the flower lines to improve efficiencies and line speeds, coaching, and mentoring the staff, doing my bit as a frontline key worker.
January 20 – April 20 • On A Roll Sandwich Company • Interim Manufacturing Manager
This role is very hands on focusing on K.P.I.’S and improving current systems that are in place, on a Roll Sandwich Company is a family run business with a 20-million-pound turnover per year, supplying Airlines, Schools, and Hospitals with over 200 Sku’s, quality and customer service is paramount, I am currently working as the Interim Manufacturing Manager until they find a suitable person to become full time in this position
October 18 – January 20 • Avara Foods Ltd •Interim Management support
Interim Management support for a very busy poultry site producing top class products to all major supermarket chains, this contract is a very hands on role and was originally for a 3 month period covering Christmas lines, this contract has now been extended 5 times now due to being very successful within my role as Production Management Support Manager, my new role is to improve K.P.I’S within the Production areas on a month by month basis and again take control of the Christmas Production lines.
February 18 – April 18 • Fei Foods Ltd •Interim Production Manager.
Running a shift pattern until the company gets a full-time Production Manager,
Maintaining K.P.I.’S and business focus at this very busy time.
Identifying waste and reducing by 7% around £4000 per week.
September 17 – December 17• Green core Food to Go • Interim Night Manufacturing Manager.
Responsible for All site functions on a busy night shift.
Promoted to Manufacturing Manager from Production Manager running the whole site on the night shift, also responsible for a few projects on day shift as well.
May 17 – September 17• Green core Food to Go• Interim Night Production Manager
Implemented I.C. into the workplace and improved efficiencies by 5% around £5000 per week by focusing on online processes.
Created a new shift reporting system to focus more on K.P.I.’S.
Introduced nightly group huddles and meetings, this in turn improved morale on shift.
Reviewing current standard ways of working and improving them where needed.
Reduced labour variances on night shift by 10 % also introduced a system to monitor.
Sept 16 – February 17 • Dawn fresh Seafood’s Ltd • Interim Site Operations Manager
Saved the company £6000 per week in labour costs by reducing shift patterns.
Introduced colour coding to improve visibility of products and in turn improved stock counts by 12.5%
Team leaders/managers were trained on metrics to enable them to focus more on quick wins which were achievable. this improved performance by 15%
5% improved online performance by implementing SIC to highlight underperformance
Introduced Wizard Air Cutting Knives which improved line yields by 2% saving £8000 per week.
April 16 – August 16 • Walker’s Deli (Samworth Brothers)• Interim Factory Manager
A major contributor in achieving the audit status of M&S Gold and Tesco Blue P.I.U.
Worked closely with Personnel to ensure a full and robust recruitment plan was in place for the recruitment of over 200 new employees for new introduced shift patterns and a new Pate extension to improve Productivity.
Jan 14 – April 16 • Moy Park • Production Manager
Increased throughput from 650,000 birds per week to 750,000 birds per week by restructuring the department and identifying better and smarter ways of working.
Reduced mechanic breakdowns from 12.7% to 7.2% by identifying major issues.
Set up a reporting system driving performance rather recording it.
Set up daily review meetings reviewing the last 24hrs / next 24hrs performance.
Set up weekly review meetings to review long term trends within the business.
Oct 10 – Dec 13 • Kerry Foods Ltd • Sleeving / High Risk Factory Shift Manager
As a project lead for a standardisation operation for Banquet lines, line mapping and process flow was introduced, this saved £40k per shift per year on labour, totalling £160K per year and reduced customer complaints by 76%.
Proactively investigated the banquet line due to very high customer complaints.
Successfully identified a packing problem and conduction a project to rectify and implement a solution which was to alter the height of the products in bags this reduced customer complaints by 76% and gave Tesco the confidence to provide more products for the production line.
Working with the Quality team to create a daily PIU checklist to improve GMP standards. This has progressed last year’s PIU status from amber to green
Reduced giveaway from 9% to the site standard 2% within 6 months by focusing on procedures and training line leaders on being more vigilant with team performance.
Significantly improved motivation and production within the team recognised by the planning team and senior management by introducing a buddy system and division of recipes to make the work more varied and interesting for the team.
Reduced walking time for the weigh room team by 50% by standardising processes and breaking down data.
Previous Job Titles Include:
De-Boning Production Manager, Area Production Manager, Night Shift Manager, Production Supervisor, Factory Chef, Factory Manager, Operations Manager, Night Site Manager, Manufacturing Manager, Managing Director, Day Site Manager, Interim Support Manager, Continuous Improvement Manager, Projects lead, Projects Manager, Interim Factory Manager, Interim Manufacturing Manager, High Risk and Low Risk Interim Production Manager, Deputy Site Manager, Interim Production Manager.
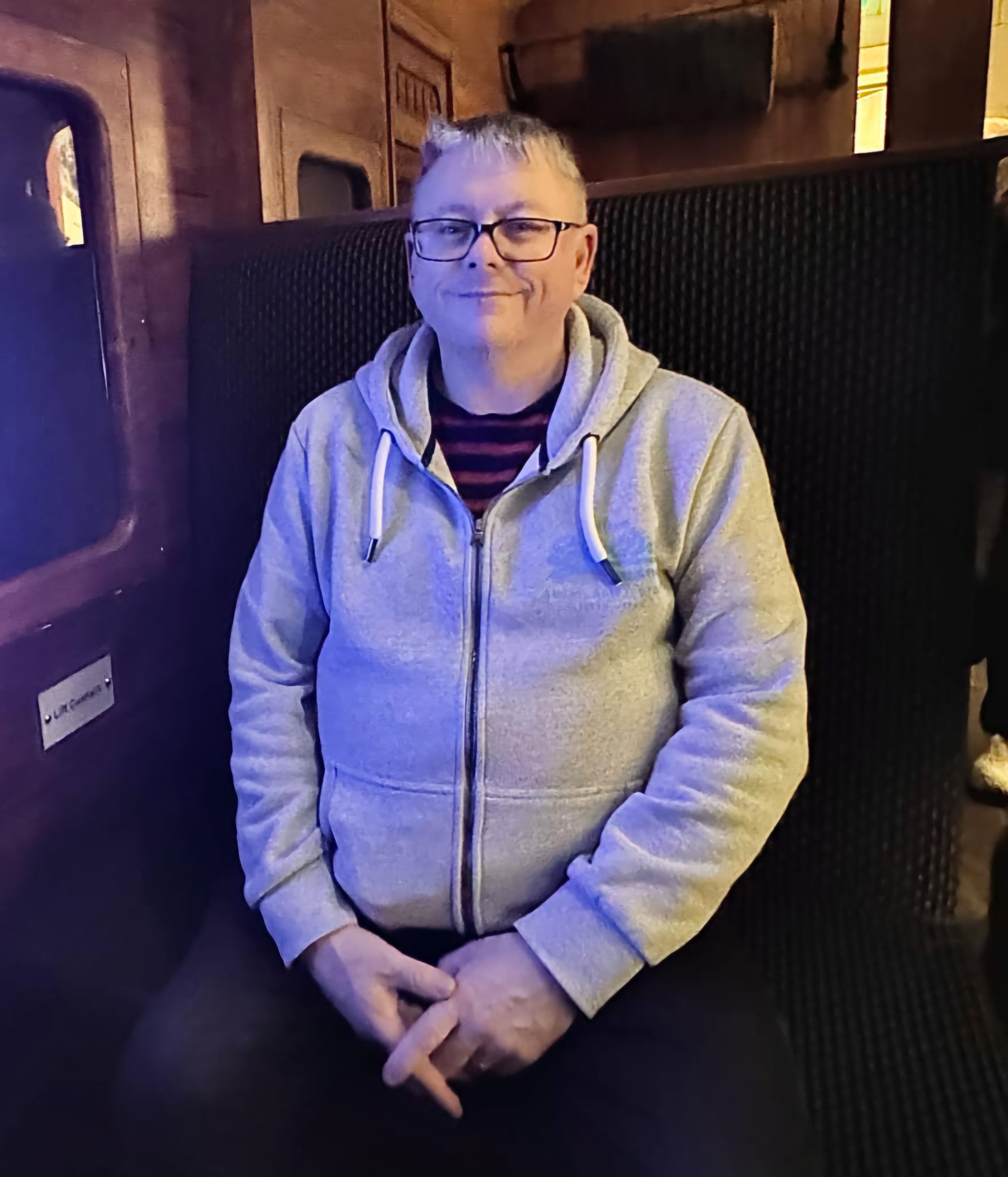
Let's Connect
If you’re looking for an experienced Interim Manager with a strong background in production management, process optimization, and team leadership, feel free to reach out. I’m always open to discussing new opportunities, collaborations, or challenges where I can bring value.
You can contact me via email at [email protected] or give me a call at 07793217890
Let’s connect and explore how my expertise can help drive success in your business. You can also find me on LinkedIn: Mark Akers.